Although the year started with cautious optimism that costs would continue to go down, the latest data from the U.S. Bureau of Labor Statistics show an increase in construction input prices. Specifically, "construction materials prices increased 0.4% in...
Reimagining Construction Materials Purchasing on Jobsites
Construction materials purchasing and management are essential elements in construction project planning and control and represent a significant expense on every project -- Big, medium, and small. It is reported that materials and required equipment make 70% of the total project cost. Therefore, improper handling and management of material through its lifecycle adversely affects the cost of the project (and trade business). Materials management is a critical function to focus on improving productivity. No matter the size of your trade contracting firm or type of project, its vital to giving attention to this area of the business.
As U.S. construction starts continue to grow in 2022, projects across the construction spectrum (industrial, residential, commercial) require improved material purchasing and management practices. Today, these practices are reimagined in easy-to-use and affordable technology, helping subcontractors deliver timely materials and equipment to the jobsite, improved planning, increased labor productivity, better schedules, and lower project costs.
With a few clicks on the desktop, tablet, or phone, StructShare is reimagining Material Purchasing and Management on Construction Jobsites across the U.S.
As stated above, construction materials represent a significant expense, so minimizing procurement or purchase costs presents substantial opportunities for reducing costs. The materials purchasing and management platform ensures that the right quality and quantity of materials are appropriately selected, purchased, delivered, and handled on-site promptly and at a reasonable cost.
Poor materials management also results in excessive and avoidable costs during construction projects. Sound material management practices include efficient material handling and equipment maintenance. On the flip side, inventory, shop fabrication, field servicing involves material handling and specific attention to reduce costs. The use of innovative equipment and software are reimagining wholesale changes not seen before in construction, but with one catch. The switchover costs for subcontractors replace antiquated practices with automated and digital workflows is minimal. For example, you don't need IT resources to implement StructShare.
The definition of material management is a series of related processes to facilitate and coordinate planning, requirements, sourcing, purchasing, transporting, storing, and controlling materials, minimizing waste, and optimizing the profitability by reducing material costs.
Building materials account for just under 70 percent of the direct cost of a project or a facility, the remaining 30 percent being the labor cost. This should be a focus of every subcontractor to optimize using purpose-built technology they can implement in a day.
What are the major components of construction material management:
- Estimating, planning, budgeting, and programming.
- Scheduling - procurement and purchasing
- Receiving & inspection
- Storage, warehousing, and inventory control
- Material transport and handling
- Managing waste
Construction materials management objectives:
- Efficient materials planning
- Purchasing, Procuring, and receiving
- Inventory control and efficient storage
- Supply and distribution chain
- Quality assurance (QA)
- Supplier and customer relations
- Improving department efficiencies
Trade contractors must establish harmony and good coordination between all stakeholders - the field, office, warehouse, accounting teams, and suppliers to fulfill these objectives. So how do you execute effectively by relying on email, calls, spreadsheets, multiple supplier websites, paper, and other old-fashioned methods? Materials purchasing and management software.
Advantages of using Material Purchasing and Management Software:
• Automating workflows in operations and jobsite
• Reduction in cost of material handling
• Reduction in the overall cost of the project
• Increase in labor productivity
• Increased time management
• Increased Quality Control (QC)
• Better relations and transparency with suppliers and customers involving materials on projects
For large subcontractors:
• Avoid delays caused by quality control team
• Transportation problems avoided with GPS-like tracking on deliveries
• Seasonal problems
For mid-sized subcontractors:
• Avoid delays caused by quality control team
• Avoid seasonal & transportation problems
• Mitigate miscommunications with labor or improper materials handling
For small subcontractors:
• Avoid delays caused by rejected materials by Quality Control team
• Transportation problems
• Addressing seasonal problems having historical data
• Eliminate communication breakdowns
• Find best-market price for materials (sending out multiple RFQs)
• Institue material purchasing and management processes automatically
• Reduce issues related to handling materials
Breaking construction materials costs:
Purchase Costs
Purchase cost is the unit purchase price of material from a third-party and includes freight and transportation costs.
For construction materials, it is common for trade contractors to seek volume-based pricing therefore reducing the unit cost as the quantity increases. Having material purchasing software, trade contractors can increase their leverage to bargain with suppliers by virtue of the transparency gained in their inventory, connecting to multiple suppliers for ordering quantities and scheduling delivery times. Requirements for just-in-time ordering is much easier to accomplish relying on the right technology to connect the entire ecosystem.
Order Costs
Order cost includes the expense of issuing a purchase order to an outside supplier. Order costs include fees for requisitions, creating purchase orders, analyzing and comparing suppliers, receiving and inspecting materials by field foreman. In addition, staff checking on orders, and maintaining records throughout the entire process. Lastly, office staff spend countless hours searching for lost or misplaced paperwork related to materials. The administrative burden is difficult to quantify, but purpose built materials purchasing software digitally tracks all documentation, providing notifications along the entire material management process. This saves substantial time and money and provides a full transparent view for all stakeholders.
Holding Costs
The holding costs primarily result from capital expenditure costs, storage, handling, shrinkage, deterioration and obsolescence. This involves capital tied up in materials held in the warehouse as inventory. Once contractors pay for the materials, borrowing costs kick in until the materials are installed and payments are received from the customer or general contractor. Storage and handling represents movement and security of materials, so storage costs may include disruption caused by delays for installation. Material obsolescence means that an item has lost its value, such as the case if specification changes occur before the product can be installed on the jobsite. Shrinkage involves inventory that is reduced overtime due to loss or theft or some other event. Finally, deterioration reflects a shift in material quality due to age or environmental degradation.
Unavailability Costs
The unavailability cost is incurred when the desired material is not available at the needed time. In manufacturing industries, unavailability cost is commonly called depletion or stock out and in 2020 and 2021, we have all certainly experience shortages that have delayed work and wasted labor resources delaying the entire project. For construction subcontractors, it's very difficult to forecast supply chain issues and provide accurate delivery estimates. Material purchasing and management software connects subcontractors directly to their warehouse and ecosystem of suppliers to create a rapid response to these types of challenges to staying on schedules.
What's the hold up with construction trade contractors?
While many larger trade contractors are leveraging some form of process and software for material purchasing and material management, they are lacking best practices and relying on software that doesn't unify stakeholders and workflows exclusively needed for construction projects.
Small to mid-sized firms are lacking awareness that there's affordable and easy to use software that is purpose-built for them to get started as quickly as the next day.
All contractors are still facing substantial issues managing material purchasing and management. The lack of material management best practices ultimately results in delay in work, project cost overruns, decrease in labor productivity and waste.
In conclusion
Even if you have a small staff, centralizing material management team coordination between the back office and jobsite can you help increase control, monitoring, and tracking materials across every project. Creating a "system of record" in the software increases awareness and accountability in the office, on the jobsite and with suppliers.
All aspects of efficient material management can be addressed using technology to quantify ROI and gains in efficiencies to improve practices and partners the trade contracting firm employs. Advanced software like StructShare helps subcontractors get control of material purchasing and management. Start today!
Get the latest insights on materials management for modern construction jobsites.

What the increase in Material Prices means to you
by Christian Erickson | Apr 12, 2024 | Trades 101 Blog, Material procurement, Construction material management, Invoicing, Materials Procurement, Job Cost Accounting
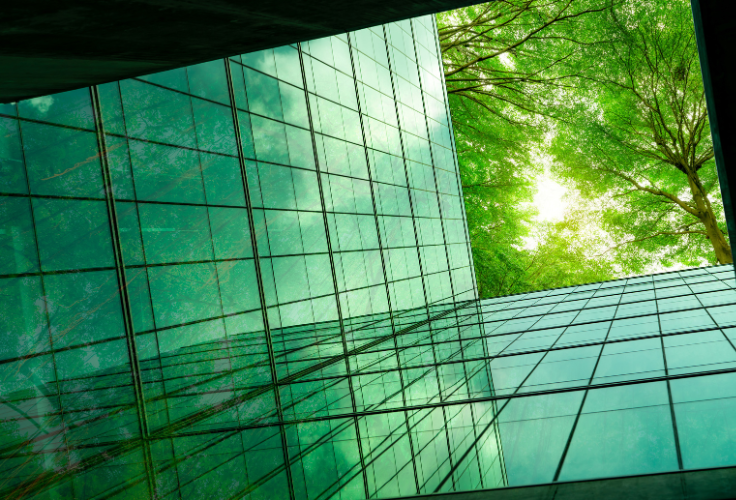
Green Building Success: Sustainable Strategies for Construction
by Lexi Garden | Mar 14, 2024 | Trades 101 Blog, News, Material procurement, Materials Management, Construction material management, Materials Procurement, Trades Blog
In the modern construction landscape, sustainability isn't just a buzzword—it's a necessity. As the industry struggles with environmental challenges, adopting green building practices becomes necessary for long-term success. We delve into actionable...
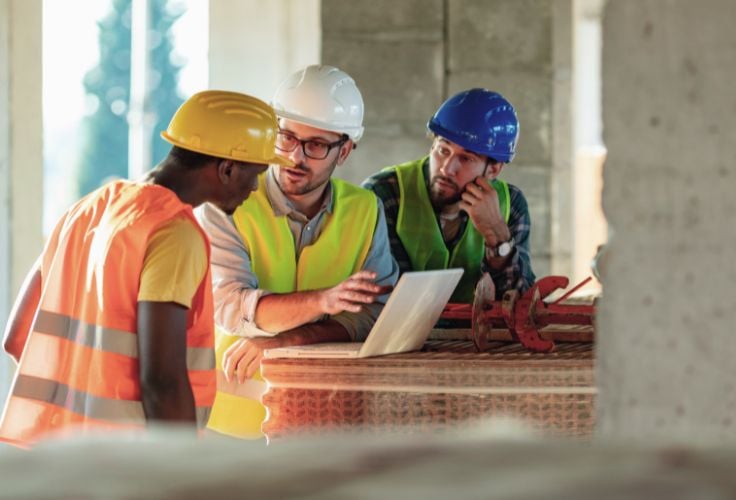
7 Reasons Technology Drives Successful Projects
by Christian Erickson | Feb 28, 2024 | Trades 101 Blog, News, Material procurement, Materials Procurement, Trades Blog
Specialty trade contractors face unique challenges in purchasing and material management that often go beyond the capabilities of basic tools like email, text, and spreadsheets. Learn why embracing more advanced tools is essential for successful projects and...