Although the year started with cautious optimism that costs would continue to go down, the latest data from the U.S. Bureau of Labor Statistics show an increase in construction input prices. Specifically, "construction materials prices increased 0.4% in...
Get More Efficiency in Your Project & Material Management Workflows
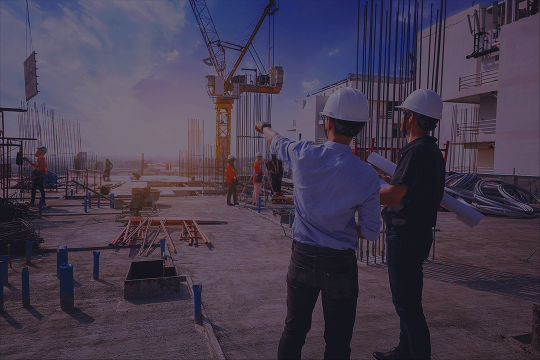
Project and material costs are skyrocketing, so how are contractors managing the headaches? Every aspect of the project is impacted by materials management – timelines, quality delays, labor, etc. It also remains one of the last areas across the construction build process that is still lagging in efficiency. When we see improvements, every aspect of the project will be accelerated and improved for all stakeholders - GCs, trades, developers, and suppliers. It's time to address the inefficiency.
Here are some tips for driving more efficiency in your project & material management workflows.
Industry challenges
Labor Streams – Continues to be a significant challenge primarily because there's been a lack of focus on materials and their effects on different labor value streams. So more than one person manages field labor, materials, takeoffs, accounting; then you bring in the fab shop with all these different silos that relate to materials from one stream to the next.
Looking at that value flow, the main focus is on managing labor, more so around materials. There hasn't been consistency. It touches so many different aspects of the business. Through the pandemic, material prices and escalations in such short periods have brought materials management to the forefront.
Subcontractors - Stakeholders, specifically material and procurement professionals, have an unaddressed legacy with the solutions. Technology such as Materials management software is helping the ones that are doing the work on jobsites. Therefore, they are one of the most important players within the entire value chain.
Technology - Connecting the field and back-office remains a priority. It's important to note that this information exchange is a two-way street; it's not about delivering information one-way; it's a back and forth. Providing the field with the right tools to enable production is a starting point. It allows multiple stakeholders and workflows to coexist on a single platform for managing materials, costs, resources that integrates with other tools (project management, accounting, estimating, etc.).
Cost of Materials: Awarded jobs with original materials estimates ten months ago are now seeing cost increases at 30% to 60% or more, creating a real sense of urgency around material management for every contractor. The time is now to grow and mature in their process and better more efficiently run their businesses.
Managing Processes - Material management can open several opportunities to sell your position from across the board. We believe there's an opportunity to educate the owners and the general contractors that trade stack. Suppose you can manage your materials and streamline a lot of these processes. In that case, it's going to ensure your ability to increase your margins because you're getting it all time you're starting to clean up, and the way you handle materials improves your ability to sell. This is a big deal!
How do we streamline the handoffs and better visibility across jobs' buying practices? But, again, this is a sign of a maturing industry that's really in the initial stages of industrialization.
Our 10 Best Practices for Delivering Efficiency
in Project & Material Management
1. Better forecasting for growth
Better forecasting requires having access to historical data used on projects. Using paper, Excel, and other manual processes creates inefficiencies that can cost you profits and your ability to forecast costs and grow your business. That's the highest cost of all and made of all the smaller costs you can't recoup. So don't let the fear of a switch keep your contracting business on the slow path with profits leaking from poorly executed material management workflows.
2. Improve delivery tracking and inventory management
There's no doubt that inventory management is essential for every trade contractor. However, employing proper processes, systems, control, and reporting. The keys to successful inventory include an excellent system catalyst, product organization from raw to finished products, a cycle counting program, the proper system part routing, and consistent production reporting.
A robust inventory management system enables your firm to accurately understand various inventory categories, stock levels, and supplier quantified. You also need trigger points for re-ordering supplies and the capability for just-in-time orders, which can save trades substantial money.
Field Labor Waste Accounts for ten or More Hours Per Week.
Field foremen can spend ten plus hours per week on wasteful administrative activities related to materials management on the jobsite because they lack the right tool. These hidden costs amount to inflated material costs, labor, and mistakes in deliveries. With materials management software, they can communicate with all stakeholders (office, field, warehouse, supplier, general contractor, accounting) with a few clicks on their phone or laptop.
3. Accurate and accessible real-time data
1. Live updates to your schedule and tasks offsite - One can use real-time collaboration technology to stay updated on jobs instead of wasting time on weekly meetings and daily tasks.
2. Fast, effective collaboration - Get your updates now. Learn about the progress now. Make changes now. That's what real-time collaboration brings you. In short, you can save time and provide your workers at the site with new information at any time.
3.Fewer emails and calls - The need to send out emails decreases through instant messages in real-time. There is also no need to call as the information is structured to understand and update progress without using the traditional calling method. All communications are audited as well.
4. Less administration and an entire audit trail - Audit trail and record of variations are a must for any contractor and client. It justifies the resources and expenses incurred that were not part of initial budget planning. However, it is a daunting task for a construction manager or project finance officer to keep all the paperwork in order.
This is where real-time technology comes to play. There is less paperwork for managers if all tasks and changes are available in black and white for them to go through. In addition, live updates make it easy to create reports of the progress made and changes applied.
5. Improves decision-making and problem-solving - Real-time information and data allow anyone at construction project sites to decide or solve a problem quickly. This will keep everyone on task and allow them to continue working with minimal delays.
Construction contractors thrive to utilize real-time data and actionable information, improving even more in the future as technology advances again.
6. Higher accuracy - Inaccurate data can cause any construction project to go past its deadline or go over budget, which is why companies are embracing real-time data and information.
4. Increase productivity in the field
StructShare's Quarterly customer satisfaction survey reports the platform dramatically saves foreman 10 hours a month on-field requisition and delivery confirmations.
- Provides real-time visibility to prevent errors, improve response rate, and quickly identify and resolve disputes.
- Provides an accurate line-item breakdown of the project, inventory, and business expenses.
- Subcontractors can receive requisitions from the field digitally, send purchase orders to vendors instantly, and auto-sync the information into their accounting system in a matter of clicks, resulting in a 50% gain in order processing efficiency.
"StructShare enables the purchasing team to spend 50% less time on processing purchase orders."
5. Eliminate manual processes in the back office
Breakaway from manual tracking processes and handling documents related to materials requires a new mindset and purpose-built software to ensure materials success. Many trade contractors have full-blown ERPs, but new to the market is an easy-to-use software for connecting all stakeholders. You also don't have to break the bank in resources, time, and money to secure the entire supply chain and materials management ecosystem. Instead, you can deploy StructShare in a matter of a day or two.
All materials documents are electronic and tracked in one single source of truth. The primary goal is a trusted web-based technology platform and mobile app for the entire team. Adoption will not happen if there's a hindrance to trusting a system among anyone on the team.
Once your team is in place and adequately trusts a system, routing the documents becomes the next primary step. The Bill of Materials or other documents must be appropriately routed to where everything backflushes correctly to leverage real-time just-in-time ordering or real-time inventory. Assemblies or parent parts must be entered and linked to child parts precisely or ongoing issues.
6. Create standardization
Standardization for your Materials Management process involves developing a standard language across projects, suppliers, cost codes, and any task or procedure relevant to the organization. Creating manual processes with standardization has always been a challenge, with people, processes, and projects continually changing from project to project.
The benefits of standardization are fundamental to implementing materials management software and include:
Fundamentally, standardization means that your employees have an established, time-tested process to use.
Decrease ambiguity and guesswork, guarantee the quality, boost productivity, and increase employee morale.
Improves clarity — because a standard process will eliminate the need for guesswork or extra searching.
Guarantees quality — because work is done in a pre-defined, optimized way.
Increases productivity — because your employees won't need to ask around or comb documentation to get answers.
Boosts employee morale because employees can take pride in mastering the process and refining their skills.
7. Real-time materials cost tracking.
Real-time, right person – The field project manager or supervisor does not have all the details and info to do their job effectively. They are getting it after the fact from ERP, which is the primary data silo and causes mistakes to occur. Even the best project managers struggle with delayed information getting to them to make the best decisions.
A solution like StructShare digitizes materials management connects the office with the field. As a result, project managers can do their jobs trusting and accessing real-time details from the Field teams and back-office working leveraging the same platform instead of relying on reports pulled from the ERP.
Get materials faster and gain better control over material costs at your fingertips.
Eliminate inefficient processes and undedicated tools used to manage the communication and workflows among the field, office, and suppliers.
- Better collaboration among stakeholders.
- Reduce mistakes at any step increase costs in late deliveries, delayed payments, and repetitive data entry.
- Connect disjointed materials workflows with materials management software enables greater collaboration.
- Managers can identify trouble spots and the top-performing suppliers with access to real-time data.
8. Seamless Integration from Material Management to Project Management
StructShare's materials management platform integrated with Procore project management is a natural fit for the trade construction ecosystem. It streamlines and automates the entire material management cycle from field purchasing, office PO, and invoice approvals to real-time cost data accurate in the project management platform.
9. Define a simple path to defined material management processes
Start small. Your goal should be to simplify your processes and communication. Materials management is such a significant factor in the entire business. The project is under-addressed, and implementing StructShare is affordable and easy to deploy for users without IT resources. This translates into minimal disruption to get started the same week of purchase.
10. Material management technology simplifies workflows
Material management technology simplifies workflows and increases collaboration and communication between the field, office, and your suppliers. In addition, collecting and accessing data will facilitate frictionless communication improvement and measurement efficiency to improve the entire value stream.
We need to evaluate materials and look at our suppliers, partners, and manufacturers, educating owners that they don't need to buy some of these materials. Then, just in time, material ordering is possible.
Get the latest insights on materials management for modern construction jobsites.

What the increase in Material Prices means to you
by Christian Erickson | Apr 12, 2024 | Trades 101 Blog, Material procurement, Construction material management, Invoicing, Materials Procurement, Job Cost Accounting
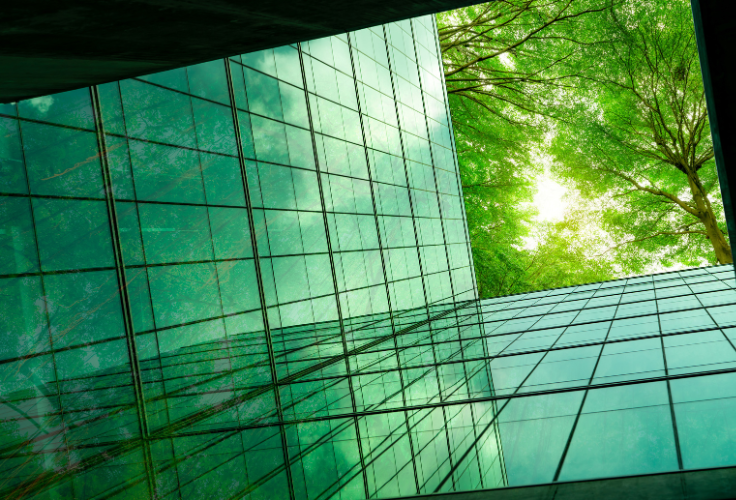
Green Building Success: Sustainable Strategies for Construction
by Lexi Garden | Mar 14, 2024 | Trades 101 Blog, News, Material procurement, Materials Management, Construction material management, Materials Procurement, Trades Blog
In the modern construction landscape, sustainability isn't just a buzzword—it's a necessity. As the industry struggles with environmental challenges, adopting green building practices becomes necessary for long-term success. We delve into actionable...
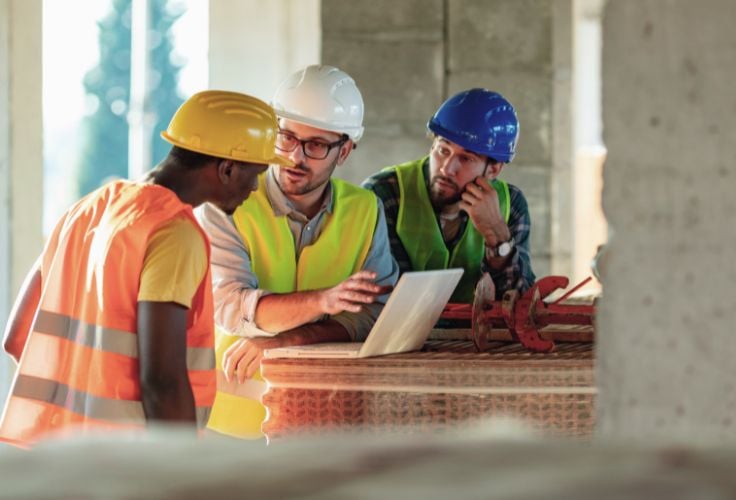
7 Reasons Technology Drives Successful Projects
by Christian Erickson | Feb 28, 2024 | Trades 101 Blog, News, Material procurement, Materials Procurement, Trades Blog
Specialty trade contractors face unique challenges in purchasing and material management that often go beyond the capabilities of basic tools like email, text, and spreadsheets. Learn why embracing more advanced tools is essential for successful projects and...